At Ontario Tech University, a team is developing an energy-efficient controlled-environment agriculture facility that will outperform traditional greenhouses in the production of strawberries—particularly during the winter months in Canada. They will be equipped with an Autonomous Intelligent Monitoring System to monitor health and growth, which will trigger early interventions if plants start to wane.
Brilliant Farm Project Plan
The emergence of controlled-environment agriculture (CEA) has offered a myriad of new opportunities for growers—with a few significant obstacles. Indoor facilities stretch the growing season into the darker, colder months, which increases productivity and can reduce dependence on food imports in cooler climates. However, operating controlled environments requires special skills, adding labour costs, and these systems have high energy needs, especially in northern regions.
A team anchored by Ontario Tech University is developing an energy-efficient controlled-environment agriculture facility (EE-CEAF) that can meet these challenges head-on while outperforming traditional greenhouses in the production of strawberries—at scale and while extending the season. “We’re going to provide affordable agricultural products and showcase what innovation can do,” says Osman Hamid, who brought the team together. “Once we solve the energy-efficiency problem and labour problem, everything will be from farm to table in a very short time.”
“We’re going to showcase what innovation can do.”
Founding Director of Creativity and Entrepreneurship at Ontario Tech University, Dr. Hamid runs Brilliant Catalyst, the university’s “on-campus incubator” for innovation and entrepreneurship. Its programs support startups founded by university students, alumni, and faculty, including project partners Turnkey Aquaponics and Moduleaf Technologies. These are Canadian solutions coming from Canadian founders and innovators. “I have the privilege of being able to see all these creative ideas and the entrepreneurial spirit that comes from a bigger community,” Dr. Hamid says. “The Homegrown Innovation Challenge speaks to what we wanted to do when we created this ecosystem.”
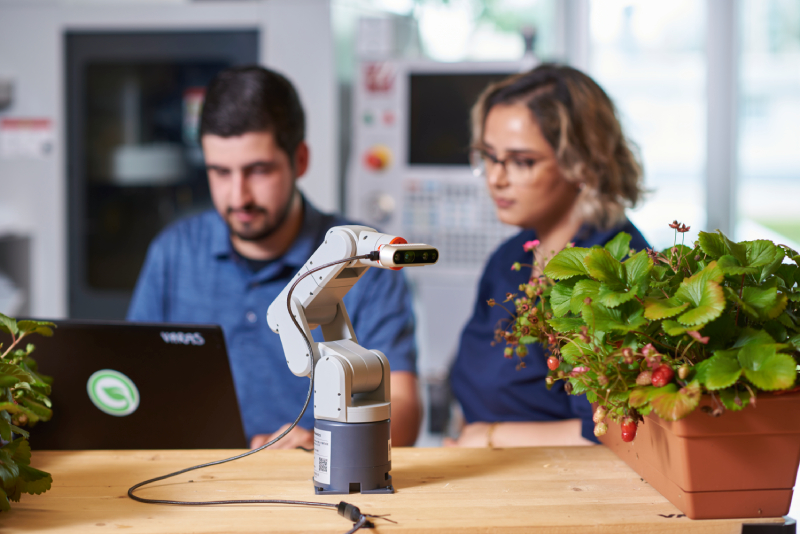
Located at Willowtree Farm in Port Perry, Ontario, the EE-CEAF facility is a thermally-enhanced greenhouse with 350 square metres of dedicated grow space. It will be tested and optimized by researchers with a broad range of expertise, from artificial intelligence to aerospace systems engineering.
According to Dr. Hamid, “Traditional farming will always have a place because farmers are the most in touch with the land. With technology, things can become more competitive. Things are more accessible at affordable costs and open doors to people who might not have seen farming as a profession.” Alex McKay, co-owner of Willowtree Farm and a second-generation farmer, agrees, noting, “The next generation doesn’t see new technology as a threat. They see it as a way to further their legacies. That is the exciting part, being able to work with new partners and grow our networks.”
“The Homegrown Innovation Challenge speaks to what we wanted to do when we created this ecosystem.”
The complementary technologies at the facility include a combined cooling, heat, and power system (CCHP), a Waste Heat Dehumidification System (WHDS), and an Autonomous Intelligent Monitoring System (AIMS). The CCHP uses organic waste to generate heat and electricity. The heat can warm the grow space or power a heat pump to cool it. The CCHP will also recycle carbon dioxide and nutrients back to the plants. The WHDS runs on captured waste heat from artificial lights providing dehumidification. Lastly, if a plant begins to wane, the AIMS that monitors its health and growth will trigger early interventions.
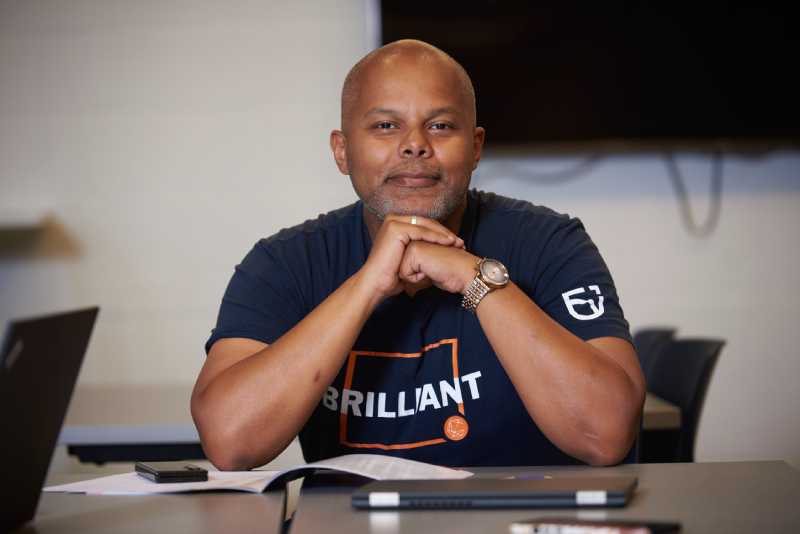
“Having integrated solutions really provides a competitive advantage,” Dr. Hamid says. “Perhaps the best thing about the project is being able to fail quickly, learn quickly, and fix it quickly. I know it sounds weird to be excited about failure, but I think the process is going to be more than fast. It’s going to be hypersonic.”
Collaborators
- Glenn Harvel, Ontario Tech University
- Connor Loughlean, Ontario Tech University
- Qusay Mahmoud, Ontario Tech University
- Alexander McKay, Willowtree Farm
- Craig Robinson, Turnkey Aquaponics Inc.
- Jaho Seo, Ontario Tech University
- Tony Veneziano, Turnkey Aquaponics Inc.
- Nicholas Varas, Moduleaf Technologies
- Michael Veneziano, Turnkey Aquaponics Inc.